Рассматривается работа массообменного оборудования процесса алкилирования изобутана олефинами. Исследование проводили с использованием моделирующей системы Honeywell UniSim Design, в которой сформировали модель установки. С целью ресурсосбережения и для обеспечения чёткого разделения компонентов алкилата предлагаются изменения в технологическую схему процесса.
Ключевые слова: алкилирование, изобутан, олефины, катализатор, моделирование, Honeywell UniSim Design.
Введение
Одним из способов производства высокооктановых неароматических углеводородов является промышленный процесс сернокислотного алкилирования изобутана олефинами [1]. Для совершенствования процесса в ряде работ исследуют возможность перехода от гомогенных к использованию твердофазных катализаторов [2–3], анализируются технологические схемы и оборудование установок [4], разрабатывают компьютерные системы для описания дезактивации катализатора [5]. На промышленных установках в зависимости от состава используемого сырья, технологических режимов и действующих на них возмущений и других воздействий возможны отклонения от регламентных значений фракционных составов технологических потоков, в частности содержания изобутана в рециркулируемой изобутановой фракции и, как следствие, для фракции н-бутановой измененное долевое присутствие изобутана, н-бутана и углеводородов С 5+ (преимущественно изопентана, н-пентана, 22-диметилбутана и 23-диметилбутана с температурами кипения 28 о С, 36 о С, 49.7 о С и 57.9 о С соответственно).
Цель работы — исследование возможности на колоннах ректификации реакционной массы алкилирования снижения энергоёмкости и предотвращения присутствия углеводородов С 5+ во фракции н-бутана, а также проведение предпроектных расчетов ректификационного аппарата с целью выделения изобутана из фракции н-бутановой, например для случаев ухудшения четкости разделения компонентов алкилата в колонне-деизобутанизаторе.
Методы
Исследования проводили с использованием моделирующей системы Honeywell UniSim Design [6], в которой сформировали модель установки сернокислотного алкилирования изобутана олефинами [7]. В качестве математического пакета для расчета термодинамических свойств компонентов фракций использовали метод Peng-Robinson.
Компонентный состав реакционной массы алкилирования (РМА) представлен в таблице 1 (используются обозначения углеводородов Honeywell UniSim Design). График ASTM D86 разгонки РМА приведен на рисунке 1, значение средней молярной массы составляет 84 кг/кмоль.
Таблица 1
Компонентный состав РМА
Наименование компонента смеси |
i-Butane, Propene, 1-Butene, cis2-Butene, tr2-Butene, i-Butene, 2M-2-butene, Propane, n-Butane, i-Pentane, n-Pentane, 22-Mbutane, 23-Mbutane, 2-Mpentane, 3-Mpentane, n-Hexane, 22-Mpentane, 24-Mpentane, 23-Mpentane, 223-Mbutane, 33-Mpentane, 2-Mhexane, 3-Mhexane, 224-Mpentane, 234-Mpentane, 23-Mhexane, 24-Mhexane, 25-Mhexane, 223-Mpentane, 2-Mheptane, 34-Mhexane, 3-Mheptane, 225-Mhexane, 234-Mheptane, 224-Mhexane, n-Decane, n-C11, n-C12, n-C13, n-C14 |
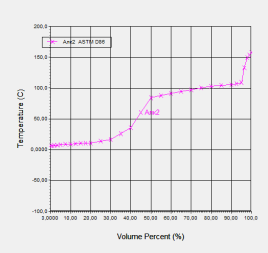
Рис. 1. График ASTM D86 разгонки реакционной массы алкилирования
На рисунке 2 показан фрагмент «типовой» технологической схемы установки сернокислотного алкилирования изобутана олефинами, демонстрирующий этапы разделения компонентов РМА.
Поток РМА (
Алк2
) поступает на 59 тарелку ректификационной колонны А1–1, предназначенной для выделения изобутана (поток
изобутан
) с целью его рециркулирования в поток питания реактора алкилирования.
Рис. 2. Фрагмент «типовой» технологической схемы установки сернокислотного алкилирования изобутана олефинами (распечатка в Honeywell UniSim Design)
В колонне используют 80 тарелок с колпачковыми контактными устройствами. С низа колонны поток ( наА1–2 ), также содержащий в смеси не отогнанный верхом изобутан, направляется на 19 тарелку ректификационной колонны А1–2, в которой происходит выделение н-бутана и поступивших в колонну остатков изобутана (поток n -бутан ). Изобутан имеет температуру кипения -11 о С, поэтому в данном аппарате отгоняется вместе с н-бутаном, температура кипения которого -0.5 о С. Отметим, что в зависимости от технологического режима работы колонны во фракции н-бутана кроме изобутана также могут присутствовать углеводороды С 5+ . Колонна содержит 40 желобчатых тарелок. Низом отбирается сырой алкилат (поток наА1–3 ), который, пройдя теплообменник, подается на 8 тарелку колонны А1–3, имеющую 20 желобчатых тарелок. С верха колонны отбирается легкий алкилат (поток авиаалк ), с низа — мотоалкилат (поток мотоалк ).
Для моделирования технологической схемы (рисунок 2) использовали следующие значения технологических параметров для потока РМА: расход 31.5 т/час, температура 62 о С, давление 710 кПа.
Сходимость расчетных процессов, выполняемых средой моделирования для колонн, получена по следующим активным спецификациям: для А1–1 — содержание изобутана в потоке, отбираемом с верха аппарата, не менее 99 % мас.; для А1–2 — содержание н-бутана в потоке верха колонны не менее 88 % мас.; для А1–3 — температура начала кипения фракции легкого алкилата Т нк_ ASTM_D86_0 %vol = 54 о С и температура конца кипения Т кк_ ASTM_D86_100 %vol = 118 о С.
Результаты и обсуждение
Для технологической схемы (рисунок 2) в моделирующей среде Honeywell UniSim Design было рассчитано (таблица 2) теоретически оптимальное аппаратурное оформление колонн с целью разделения компонентов РМА, разгонка которой показана на рисунке 1. В этой таблице также приведены рассчитанные по модели целесообразные значения режимных параметров для существующих колонн с учетом их конструкции (используемое число тарелок в аппарате, тип контактного устройства), а профили температур по высоте аппаратов показаны на рисунке 3.
Таблица 2
Рассчитанные значения конструкционных и режимных параметров колонн *
Колонна |
Р кон , кПа |
Р реб , кПа |
R min R |
N min |
N акт N |
N opt N пит |
Т кон , о С |
Т реб , о С |
А1–1 оптимальная промышленная |
650 —”- |
710 —”- |
15.7 17.0 |
37 — |
88 80 |
65 59 |
48.2 48.3 |
102.9 100.7 |
А1–2 оптимальная промышленная |
415 —”- |
420 —”- |
1.3 1.5 |
29 — |
67 40 |
15 19 |
42.9 42.1 |
138.1 138.2 |
А1–3 оптимальная промышленная |
120 —”- |
130 —”- |
0.7 1.6 |
10 — |
20 20 |
2 8 |
76.5 80.7 |
127.4 150.1 |
* Обозначения: Р кон и Р реб — давление в конденсаторе и ребойлере; R min и R — минимальное и применяемое в расчетах флегмовое число; N min и N акт — минимальное и актуальное число тарелок; N — число тарелок в промышленном аппарате; N opt и N пит — оптимальная и используемая в расчетах тарелка питания; Т кон и Т реб — температура в конденсаторе и ребойлере.
Рис. 3. Температурный профиль по высоте аппарата:
(а) — колонна А1–1; (b) — колонна А1–2; (с) — колонна А1–3
Как отмечено выше, в промышленных ректификационных колоннах используются колпачковые и желобчатые контактные устройства [7], эффективность которых составляет величину порядка 0.5÷0.6. С учётом приведенного показателя эффективности ниже проводится сравнение конструкционных параметров промышленных колонн с соответствующими теоретически оптимальными оценками из таблицы 2.
Промышленные колонны А1–1 и А1–3 по сопоставляемым показателям имеют значения достаточно близкие к теоретически оптимальным, что позволяет в практических условиях при правильной настройке технологических режимов достигать требуемую четкость выделения изобутана из РМА и разделения легкого и мотоалкилатов соответственно.
В промышленной колонне А1–2 используют существенно меньшее (40 шт.) по сравнению с оптимальным (67 шт.) количество тарелок, что может приводить к большой (по сравнению с другими колоннами) параметрической чувствительности аппарата к изменению технологических параметров.
Результаты моделирования рассматриваемой технологической схемы с конструкционными параметрами колонн действующей установки приведены на рисунке 4 в виде графиков ASTM D86 разгонки целевых фракций. Анализ полученных расчетных результатов показывает, что для рассматриваемого состава РМА (рисунок 1) демонстрируется достаточно четкое разделение фракций легкого и мотоалкилатов.
В соответствии с СТП 2059–2001 во фракции изобутановой циркулирующей не нормируется содержание н-бутана, следовательно в кубовом продукте, отбираемом с низа колонны А1–1 и поступающим на питание колонны А1–2, будут одновременно присутствовать изо- и н-бутаны, соответственно марка фракции н-бутановой, отбираемой с верха колонны А1–2, во многом определяется четкостью выделения изобутана в колонне А1–1.
Рис. 4. Графики ASTM D86 разгонки: (а) — авиаалкилат М вес = 103.5 кг/кмоль, ρ 20 = 690 кг/м 3 ; (b) — мотоалкилат М вес = 131.4 кг/кмоль, ρ 20 = 725 кг/м 3
Сказанное необходимо учитывать при оценке целесообразных режимов работы колонн.
Для оценки принципиальной возможности рекуперации тепла потоков схемы было рассмотрено влияние температуры потока питания колонны А1–2 на чёткость разделения компонентов смеси. Расчеты показали, что при уменьшении температуры потока питания от 100 о С до 20 о С содержание углеводородов С 5+ в потоке н-бутана уменьшается с 0.489 %мас. до 0.003 %мас., то есть для промышленных условий поддерживание низких температур потока питания не дает возможность присутствия С 5+ во фракции н-бутана и одновременно делает возможным использование отбираемого тепла потока для нагревания другого технологического потока. Из таблицы 2 видно, что поток с низа колонны А1–1, являющийся потоком питания колонны А1–2, имеет температуру порядка 101÷102 о С, следовательно, имеется возможность, снизив температуру потока питания (например, до 62 о С), передать его теплоту другому потоку (например, потоку питания колонны А1–1). Отмеченное позволяет снизить энергопотребление на установке.
Предлагаемая технологическая схема показана на рисунке 5, на которой рекуперация теплоты обеспечивается включением в схему теплообменника Т-100.
Для моделируемой установки также представляет интерес рассмотрение вопроса четкости разделения углеводородов изобутан-бутан. Это связано с тем, что в технологическом регламенте для потока изобутана рециклового допускается содержание изобутана более 50 %мас. Содержание изобутана менее 99 %мас. (поток изобутан , рисунок 5) возможно из-за изменения состава РМА, некорректной настройки режимов работы колонны под конкретный состав потока питания и других факторов. В этом случае соответствующее большое количество изобутана поступит в колонну А1–2, с верха которой отбираемый поток n -бутан будет включать весь поступивший в колонну изобутан. Изобутан является реактантом процесса алкилирования, поэтому его необходимо отделить от н-бутана и возвратить на питание реактора алкилирования.
С целью разделения бутанов возможно включение в технологическую схему дополнительной колонны +Кдоп (рисунок 5).
Рис. 5. Фрагмент измененной технологической схемы установки сернокислотного алкилирования изобутана олефинами (распечатка в Honeywell UniSim Design)
Расчеты показали, что для формирования потока рец_ iC 4 с содержанием изобутана 95 %мас. может быть использована колонна со следующими конструкционными и режимными параметрами: число клапанных тарелок 37 (эффективность контактного устройства 0.75), тарелка питания 26, давление верха и низа 160 кПа и 170 кПа соответственно, флегмовое число не ниже 30, температурный профиль по высоте аппарата показан на рисунке 6а. Расчет потоков фаз по высоте колонны (рисунок 6b) и оценка геометрических размеров исчерпывающей и укрепляющей частей показали на возможность использования аппарата одного диаметра.
Рис. 6. Графики изменения технологических характеристик по высоте колонны +Кдоп: (а) — температурный профиль в о С; (b) — потоки жидкой и паровой фаз в кг/час (распечатка в Honeywell UniSim Design)
Заключение
Проведенный вычислительный эксперимент позволяет сделать следующие выводы.
Для обеспечения энергосбережения при ректификационном разделении компонентов РМА предложено включение в технологическую схему дополнительного рекуперативного теплообменника, обеспечивающего нагревание потока питания колонны А1–1 (для рассматриваемой схемы с 20 о С до 62 о С) охлаждением потока питания колонны А1–2.
С целью разделения бутанов, отбираемых с верха колонны А1–2, предложено использовать дополнительную ректификационную колонну, обеспечивающую чёткое выделение изобутана для его возврата на питание реактора алкилирования.
Литература:
- Алкилирование. Исследования и промышленное оформление процесса / Под ред. Л. Ф. Олбрайта и А. Р. Голдсби. — Пер. с англ. / Под ред. В. Г. Липовича. — М.: Химия, 1982. — 336 с.
- Солодова Н. Л., Хасанов И. Р. Перспективные процессы алкилирования изопарафинов олефинами // Вестник технологического университета. — 2015, т.18, № 9, с. 117–121
- Шириязданов Р. Р. Научно-прикладные основы процесса алкилирования изобутана олефинами на цеолитсодержащих катализаторах: Дисс. д-ра техн. наук. Уфа, 2017. — 409 с.
- Солодова Н. Л., Хасанов И. Р. Анализ работы установки HF-алкилирования ООО «ЛУКОЙЛ-НИЖЕГОРОДНЕФТЕОРГСИНТЕЗ» // Вестник технологического университета. — 2015, т.18, № 7, с. 119–123
- Ушаков А. С., Долганова И. О., Долганов И. М. Разработка компьютерной моделирующей системы процесса сернокислотного алкилирования изобутана олефинами с учетом дезактивации катализатора // Материалы XVIII Международной научно-практической конференции студентов и молодых ученых «Химия и химическая технология в XXI веке», Томск, 29 мая — 01 июня 2017. — Томск: НИ ТПУ, 2017 — с. 556
- Honeywell, Unisim Design User Guide, 2013
- Технологический регламент установки сернокислотного алкилирования ТР 24–36, ОАО «КНПЗ», 2013 г.